PTC Thermistors Manufacturing Process and Quality Control
PTC thermistors manufacturing starts from mixtures of barium carbonate, titanium oxide and other materials whose composition produces the desired electrical and thermal characteristics are ground, mixed and compressed into disks or rectangle shape, then sintered, preferably at temperatures below 1400 °C. Afterwards, they are carefully contacted, provided with connection elements depending on the version and finally coated or encased.
The major PTC Thermistors Manufacturing Process and Quality Control is as following
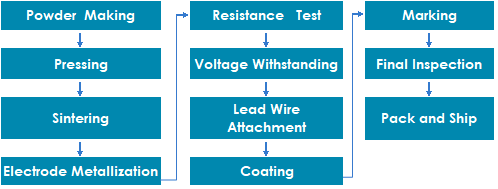
PTC Thermistor Manufacturing Process
Powder Making
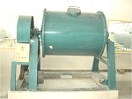
Ball Milling Mixing Equipment
Deionized Water Making
PTC thermistors manufacturing stars with Powder making.
The raw material barium carbonate, titanium oxide and other materials is precisely weighed, proportioned, mixed with deionized water, ball milling. Through ball milling mixing, the materials are evenly blended. Then powder drying, spray granulation.
The PTC thermistors powder appearance, water content, fluidity, density, as well as its electrical performance shall be carefully checked before entering the next step.
Pressing
PTC Pressing
Put the powder into the pressing machine, compressed into pills, disks, rods, slabs upon application.
The pills appearance, dimension and weight shall be carefully checked.
Sintering
Sintering Workshop
Tunnel Kiln
Disks lined in the crucible bowl, fired in the sintering kiln. Through high temperature sintering, semi conductance shall be realized, the resistance value comes into being.
Appearance, resistance, voltage withstanding shall be checked after sintering.
Electrode Metalization
PTC Electrode Saturation
Bottom Ohmic Electrode and surface electrode shall be made through silver printing, silver baking, Electrode saturation.
Appearance, ohm contact, solderability, adhesion shall be checked after electrode process.
Resistance Grouping Test
Leaded PTC Resistance Test
PTC Chips Resistance Test in Work
PTC thermistors resistance @25C goes through 100% test 3 times.
First time, each PTC chips is tested and grouped by chip testing machine.
Later the finished part with pins shall be 100% tested by machine and also manually.
Voltage Withstanding Test
Leaded PTC Voltage Test
PTC Chips High Pot Test
PTC thermistors chips is 100% high pot test, check each PTC chip, discard unqualified parts.
Qualified PTC thermistors chips request no breakdown, no Flashovers carbonization blacken, no crack, no chip contamination.
Some PTC thermistors parts may select finished part with pins 100% high pot test.
Lead Wire Attachment
Lead Wire Attachment Workshop
In some cases the PTC thermistors are sold in chip form and do not require lead wires, however in most cases, lead wires are required.
The PTC thermistors chips are inserted into the pre made tape wire, then soldering by either immersion soldering, or manual soldering.
After soldering, the parts shall go through ultrasonic cleaning.
Coating
Some PTC thermistors parts do not request coating, most parts shall request protective resin coating.
PTC thermistors chips shall be evenly coated, no bubble.
Marking
Some PTC thermistors parts request marks for identification.
Final Inspection
Appearance and resistance @25C of PTC thermistor shall be 100% checked.
Sampling test for lead wire tensile, non-trip current, RT characteristics.
Telecom application PTC thermistors may request Lightning strike wave Current waves: 10/1000μS test. Induction voltage current withstanding test.
Lighting application PTC thermistors may request simulation switch on-off life test.
Pack and Ship
All PTC thermistors and assemblies are carefully packaged and labelled. The standard lead wire PTC thermistors package can be loose bulk package or box tape package.